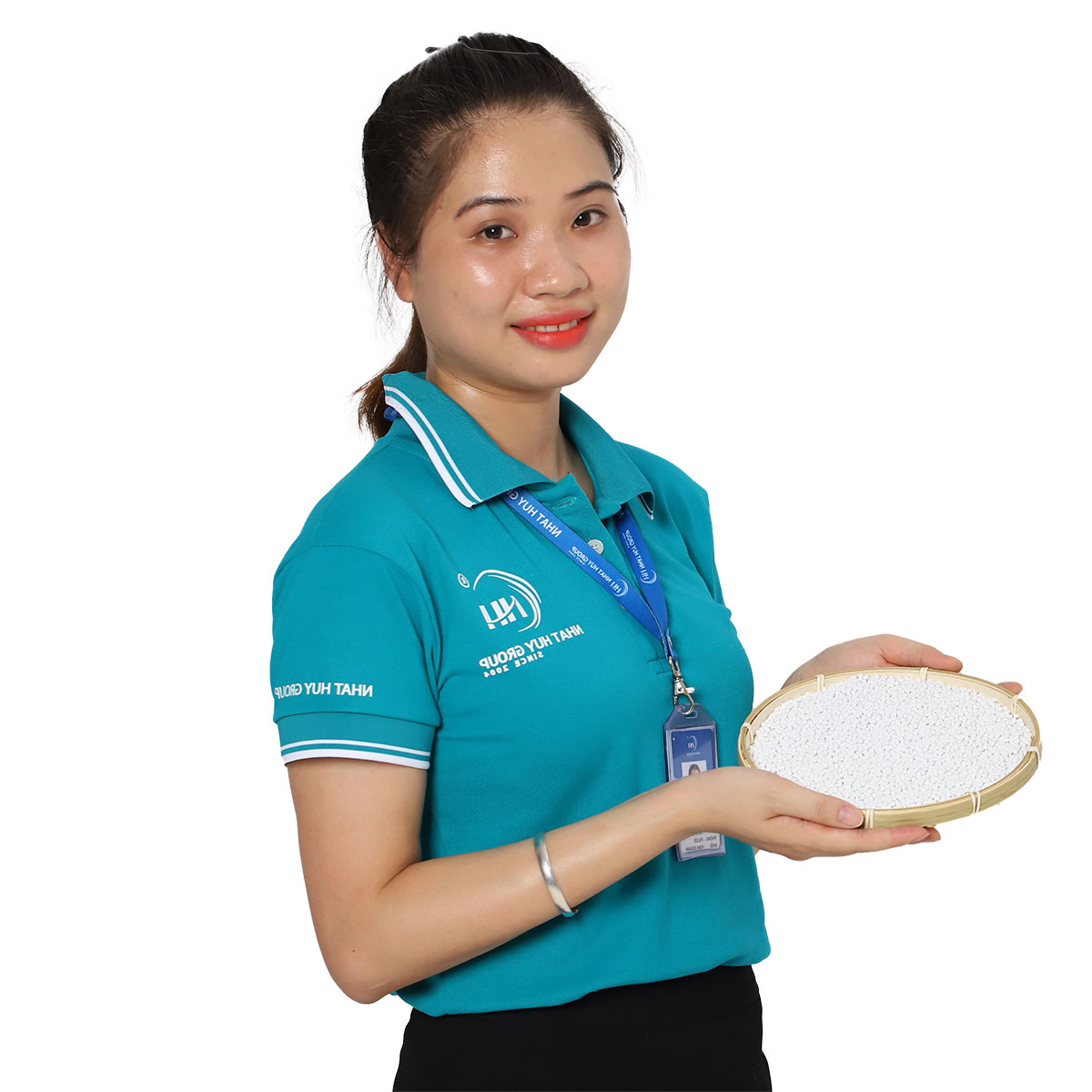
INTRODUCTION TO CACO3 FILLER MASTERBATCH
What is CaCO₃ Filler Masterbatch?
CaCO3 Filler Masterbatch is a concentrated plastic pellet composed primarily of high-purity, ultra-fine Calcium Carbonate (CaCO_3) powder, uniformly dispersed in a virgin polymer base (commonly Polyethylene – PE or Polypropylene – PP) along with specialized additives. These additives enhance the compatibility between the calcium carbonate powder and the base resin, improve dispersion, and aid in the product manufacturing process.
Other common names for this product include:
- Taical Filler
- Calcium Carbonate Additive Masterbatch
- Filler Masterbatch
Role and Importance in the Plastics Industry
The development and widespread application of CaCO3 Filler Masterbatch have marked a significant advancement in the plastics industry:
- Optimal Cost-Saving Solution: This is its most prominent benefit. By replacing a substantial portion of expensive virgin resin with much lower-cost CaCO3 powder, businesses can significantly reduce raw material costs, thereby enhancing their market competitiveness.
- Improvement of Physical and Mechanical Properties of Plastic Products: Beyond cost reduction, CaCO3 Filler Masterbatch also contributes to enhancing several important characteristics of the final product, such as:
- Increased rigidity and dimensional stability.
- Improved surface flatness and gloss.
- Enhanced printability and ink adhesion.
- Reduced shrinkage and warping after processing.
- Increased heat resistance (in some cases).
- Contribution to Environmental Friendliness: The use of CaCO3 filler masterbatch helps reduce the amount of petroleum-based polymer resin needed to produce a unit of product, thereby indirectly lowering carbon emissions and environmental impact.
Key CaCO3 Filler Masterbatch Product Lines at Mega Plast
Understanding the diverse market needs and specialized applications within the plastics industry, Mega Plasst is proud to offer two primary lines of CaCO3 Filler Masterbatch, optimized for specific base resins
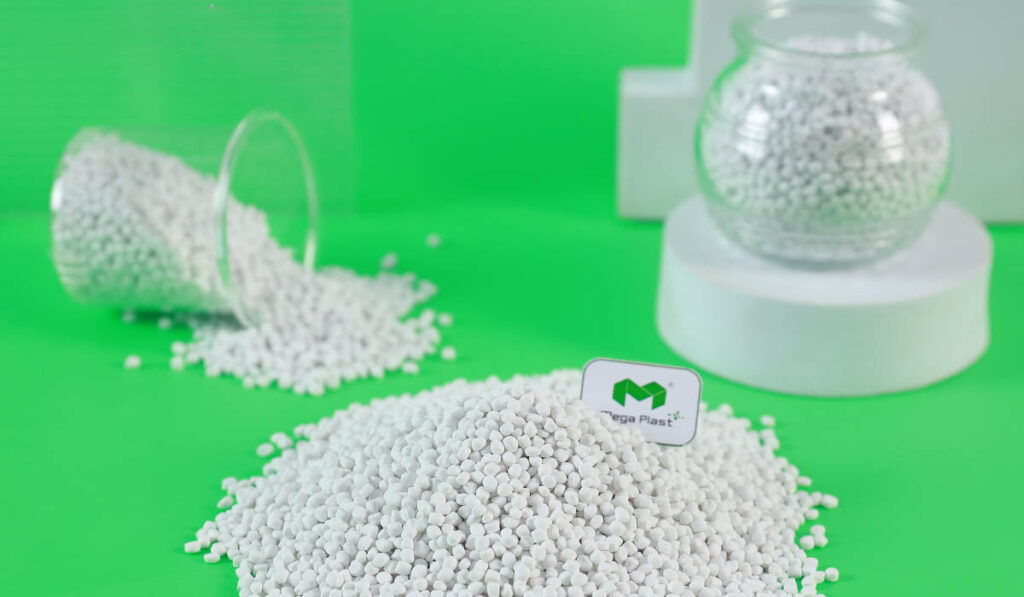
In PE, a widely used plastic for packaging, household goods, and many other applications, CaCO3 filler masterbatch not only significantly reduces raw material costs but also improves the durability, hardness, and impact resistance of the products. Specifically, in the packaging sector, using CaCO3 filler can enhance the whiteness and glossiness of the products, resulting in more attractive packaging.
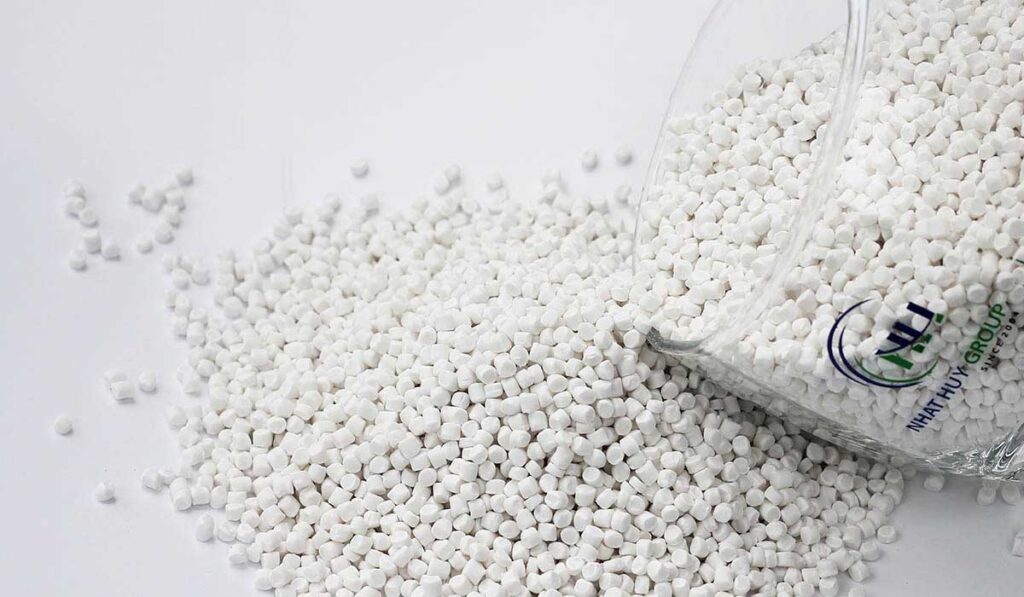
PP, known for its stiffness and good heat resistance, when combined with CaCO3 filler masterbatch, allows for the production of products with high mechanical strength, thermal durability, and chemical stability. This makes PP enhanced by CaCO3 an ideal choice for applications such as household appliances, automotive components, and construction materials where durability and resistance are crucial.
CaCO3 filler masterbatch is an effective filler solution in the plastics industry, specially optimized for two widely used types of plastics: Polyethylene (PE) and Polypropylene (PP). Each of these plastics benefits distinctively from the incorporation of CaCO3 filler masterbatch, from reducing production costs to enhancing the physical properties of the final plastic products. Each product line is developed with a unique formulation, ensuring consistent quality, high compatibility, and optimal efficiency for our customers’ production processes.
PE CaCO3 Filler Masterbatch
Mega Plast’s PE CaCO3 Filler Masterbatch is a specialized solution designed to optimize costs and enhance the quality of products made from Polyethylene (PE) resin. Combining high-quality, ultra-fine CaCO_3 powder with a PE base resin and special additives, our product ensures superior performance and stability during the production process.
Product Description
- Main Components: Ultra-fine Calcium Carbonate (CaCO_3) powder (with tightly controlled particle size), Polyethylene base resin (e.g., LLDPE, HDPE, LDPE), and additives that enhance dispersion, compatibility, and processing aid.
- General Outstanding Features:
- High loading capability, effectively reducing material costs.
- Excellent dispersion of CaCO_3 powder in the PE resin matrix, preventing agglomeration.
- Extremely low moisture content, ensuring the quality of the final product.
- Improves whiteness and surface smoothness of the product.
- Friendly to processing equipment.
Superior Benefits of Using Mega Plast's PE CaCO3 Filler Masterbatch
- Optimized Production Costs: Significantly reduces the amount of virgin PE resin used, directly lowering the cost of the final product and increasing competitive advantage.
- Enhanced Finished Product Quality:
- Increased Stiffness and Dimensional Stability: Makes products more rigid and less prone to deformation.
- Improved Surface Finish: Creates a smoother product surface, enhancing aesthetics and facilitating printing processes (referencing “Good printability,” “Smooth surface” from Mega Plast catalog page 7).
- Reduced Shrinkage: Minimizes plastic shrinkage after cooling.
- Improved Production Efficiency:
- Uniform Dispersion: Mixes easily and disperses evenly within the PE resin blend, ensuring product homogeneity.
- Increased Productivity: May help reduce cooling cycle times in some molding processes due to the better thermal conductivity of CaCO_3.
Common Applications
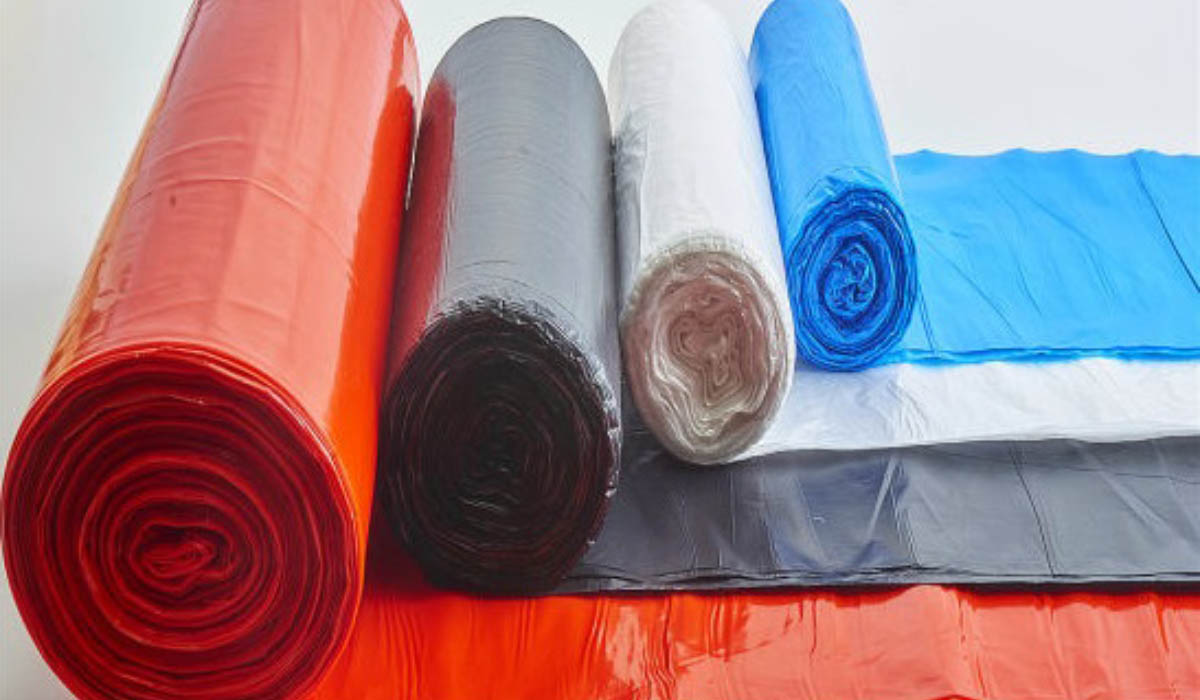
Blow Film Application
- 🟢 Shopping bags, garbage bags, T-shirt bags.
- 🟢 Agricultural films, greenhouse films.
- 🟢 Stretch films, pallet wrap films.
- 🟢 Industrial liners.
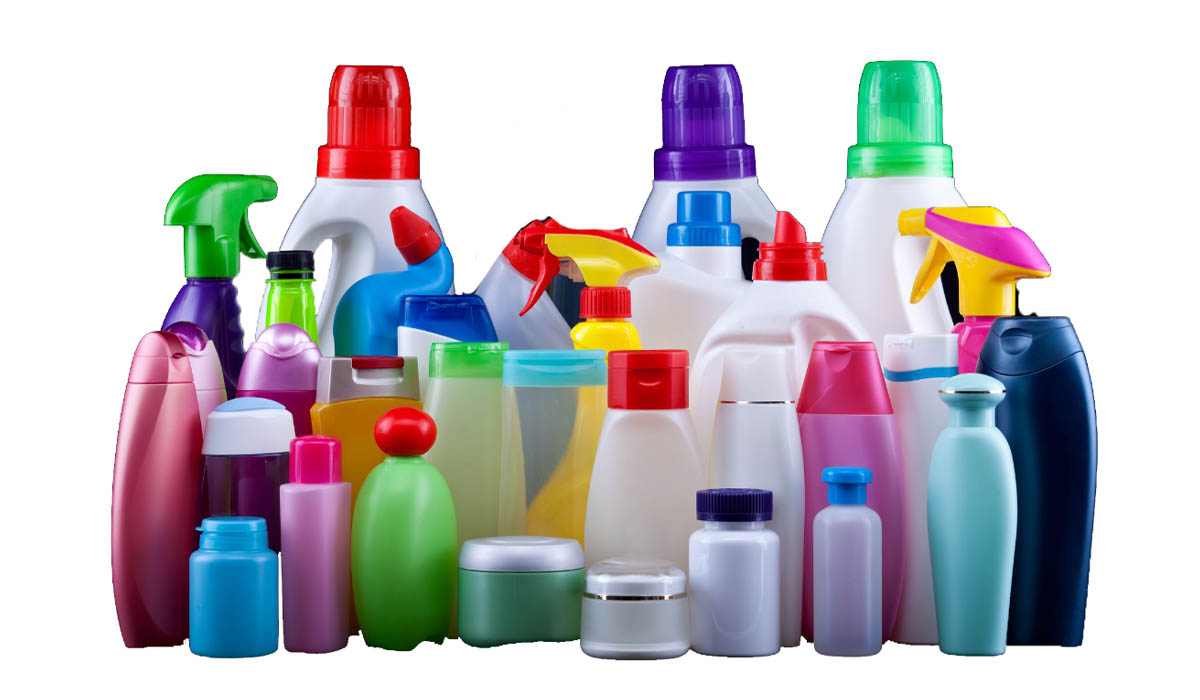
Blow Molding Application
- 🟢 Bottles for cosmetics, food, pharmaceuticals.
- 🟢 Jerry cans, small to medium-sized containers.
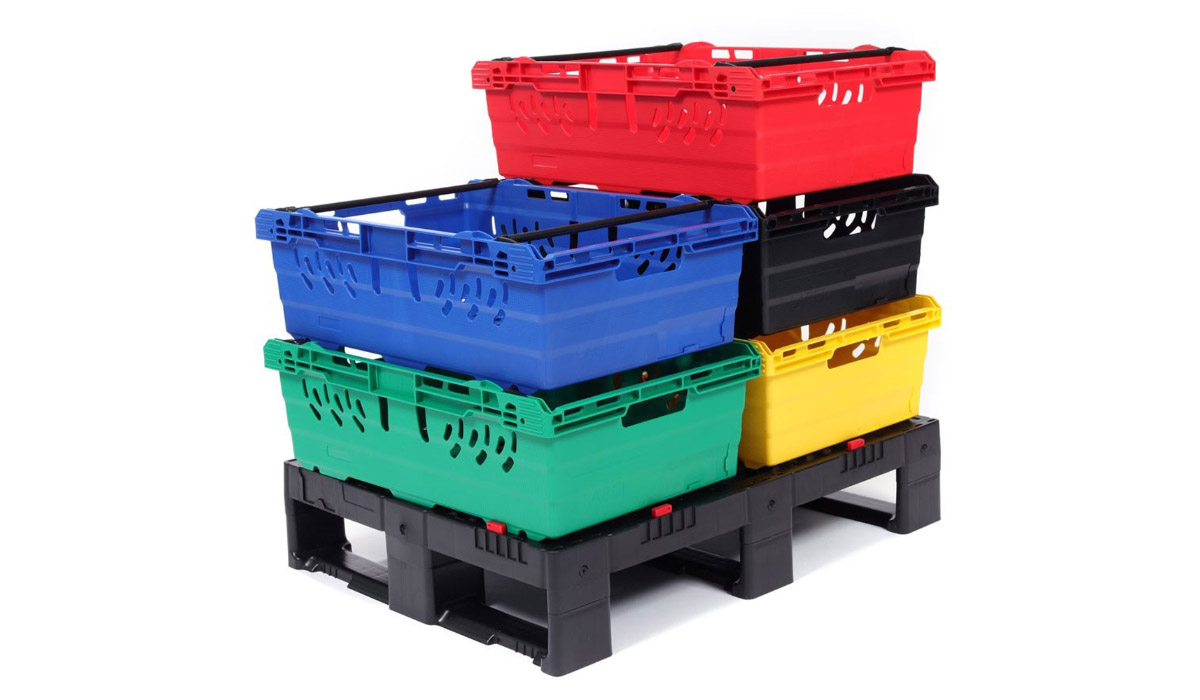
HDPE Injection Molding
- 🟢 Household items: baskets, basins, buckets, pots.
- 🟢 Plastic pallets, corrugated plastic crates.
- 🟢 Bottle caps, simple technical parts.
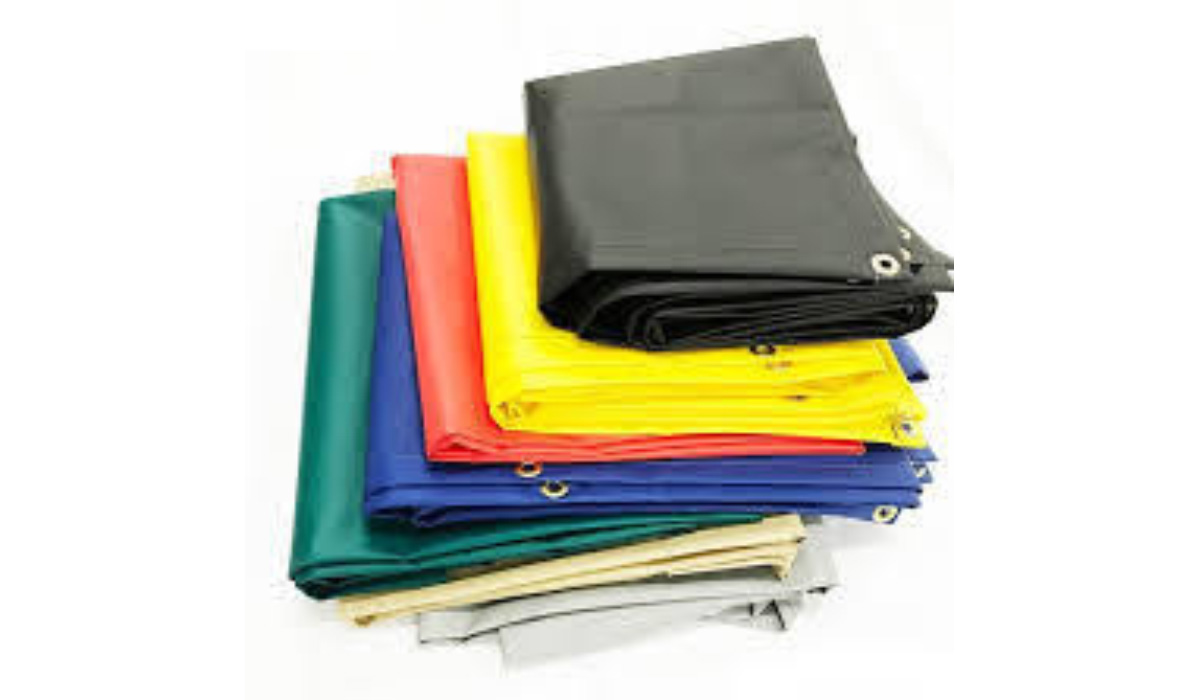
Tarpaulin
- 🟢Weatherproof sheets, construction tarps, agricultural tarps..
PP CaCO3 Filler Masterbatch
Mega Plast’s ‘s PP CaCO3 Filler Masterbatch is an advanced solution specifically researched and developed for applications using Polypropylene (PP) base resin. This product not only helps manufacturers optimize raw material costs but also significantly contributes to improving many crucial properties of the final PP plastic products, meeting the stringent demands of the market.
Product Description
- Main Components: Ultra-fine Calcium Carbonate (CaCO_3) powder (with tightly controlled particle size), Polyethylene base resin (e.g., LLDPE, HDPE, LDPE), and additives that enhance dispersion, compatibility, and processing aid.
- General Outstanding Features:
- High loading capability, effectively reducing material costs.
- Excellent dispersion of CaCO_3 powder in the PE resin matrix, preventing agglomeration.
- Extremely low moisture content, ensuring the quality of the final product.
- Improves whiteness and surface smoothness of the product.
- Friendly to processing equipment.
Superior Benefits of Using Mega Plast's PP CaCO3 Filler Masterbatch
Maximum Cost-Effectiveness: Minimizes the amount of virgin PP resin required, helping businesses save on input costs and increase price competitiveness.
- Enhanced PP Product Properties:
- Increased Strength and Stiffness: Makes products more robust and durable during use (referencing “Enhance strength,” “Excellent elongation” from Mega Plast catalog page 11).
- Improved Dimensional Stability: Products maintain their shape better under the influence of temperature and external forces.
- Attractive Surface, Easy to Print: Creates products with a smooth, glossy surface (depending on type and usage level), ideal for applications requiring high aesthetics and printability.
- Optimized Production Process:
- Excellent Dispersion: The filler disperses uniformly in the PP resin matrix, without causing filter clogging or affecting machinery.
- Improved Cycle Times: In some cases, the better thermal conductivity of CaCO_3 can help shorten cooling times, increasing productivity.
Common Applications
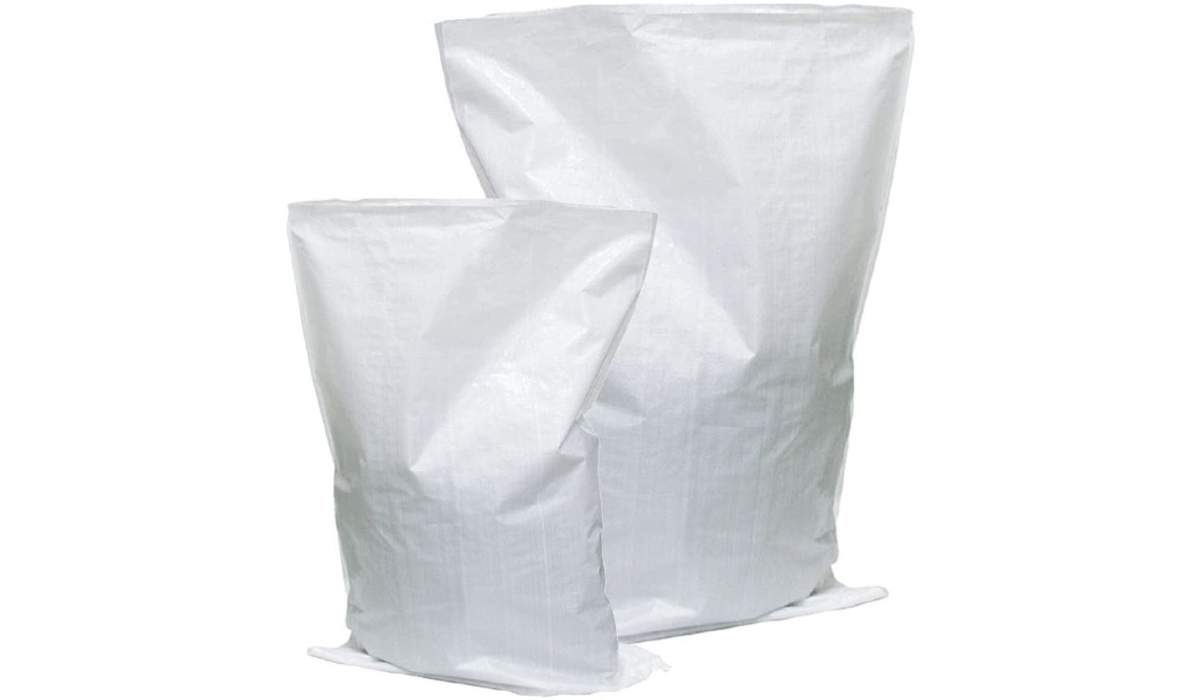
Woven/Raffia
- 🟢 PP woven bags for agricultural products (rice, coffee, pepper, etc.), animal feed, fertilizers, cement.
- 🟢 Woven geotextiles.
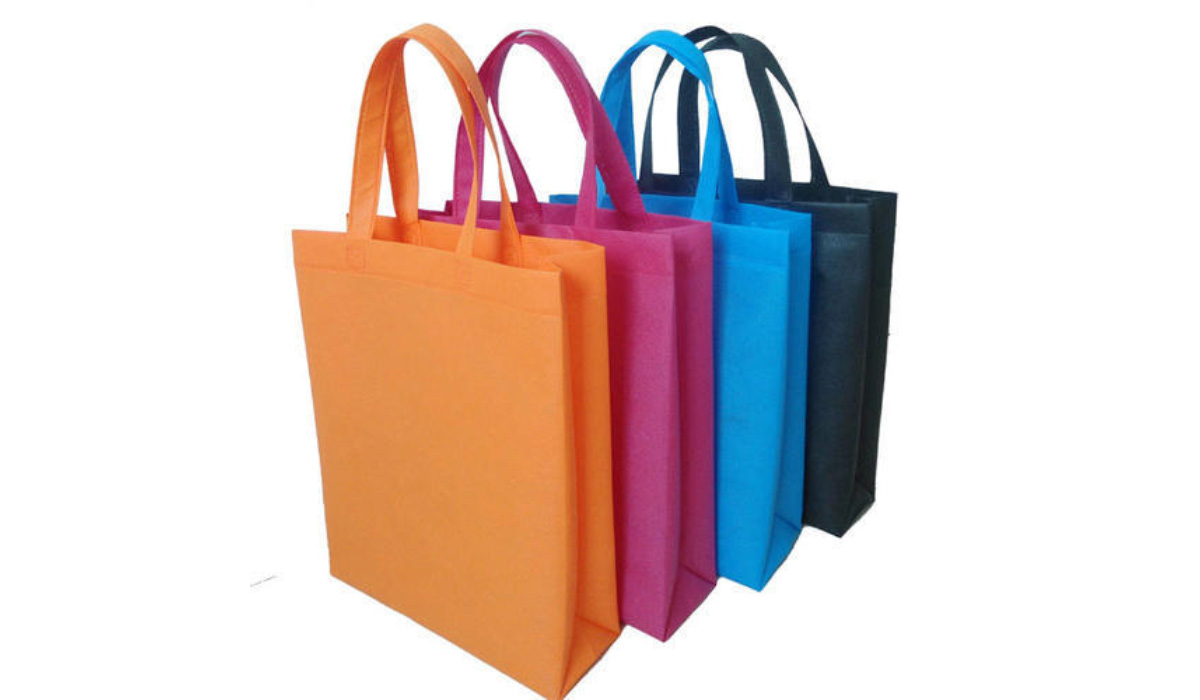
Non-Woven Fabric
- 🟢 Non-woven shopping bags, promotional bags.
- 🟢 Liners for agricultural and industrial use.
- 🟢 Medical applications: face masks, surgical gowns, diapers.
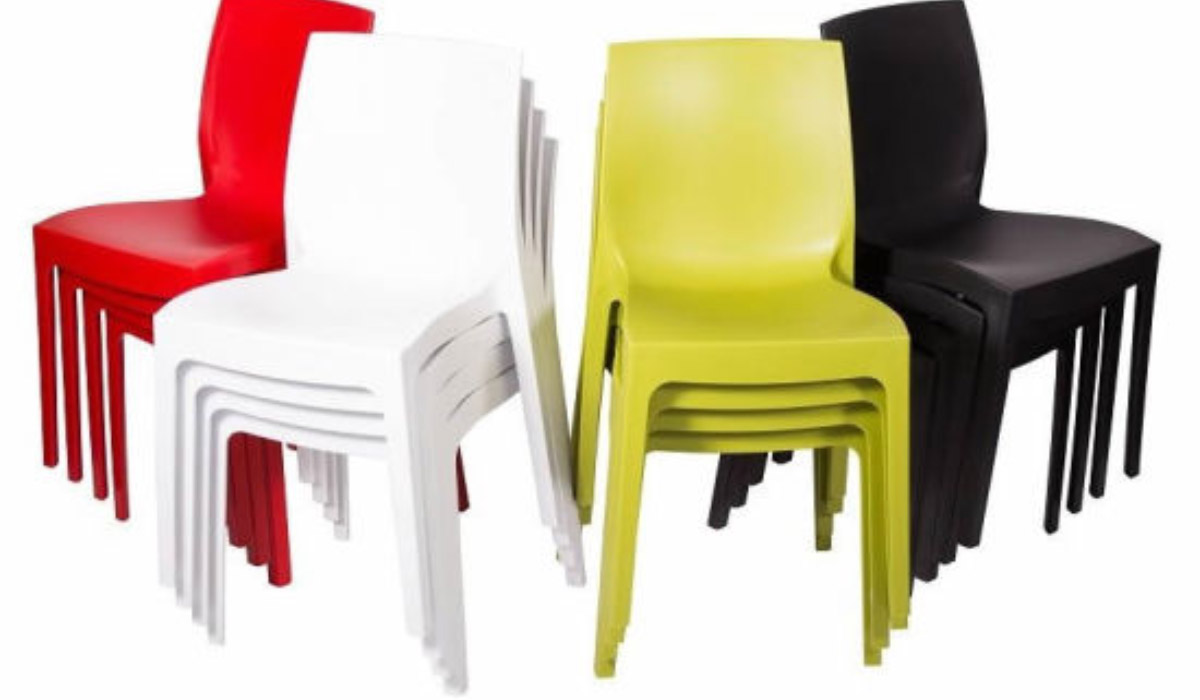
Injection Molding
- 🟢 Household items: tables, chairs, containers, food boxes, buckets..
- 🟢 Automotive and motorcycle parts.
- 🟢 Plastic pallets, industrial crates.
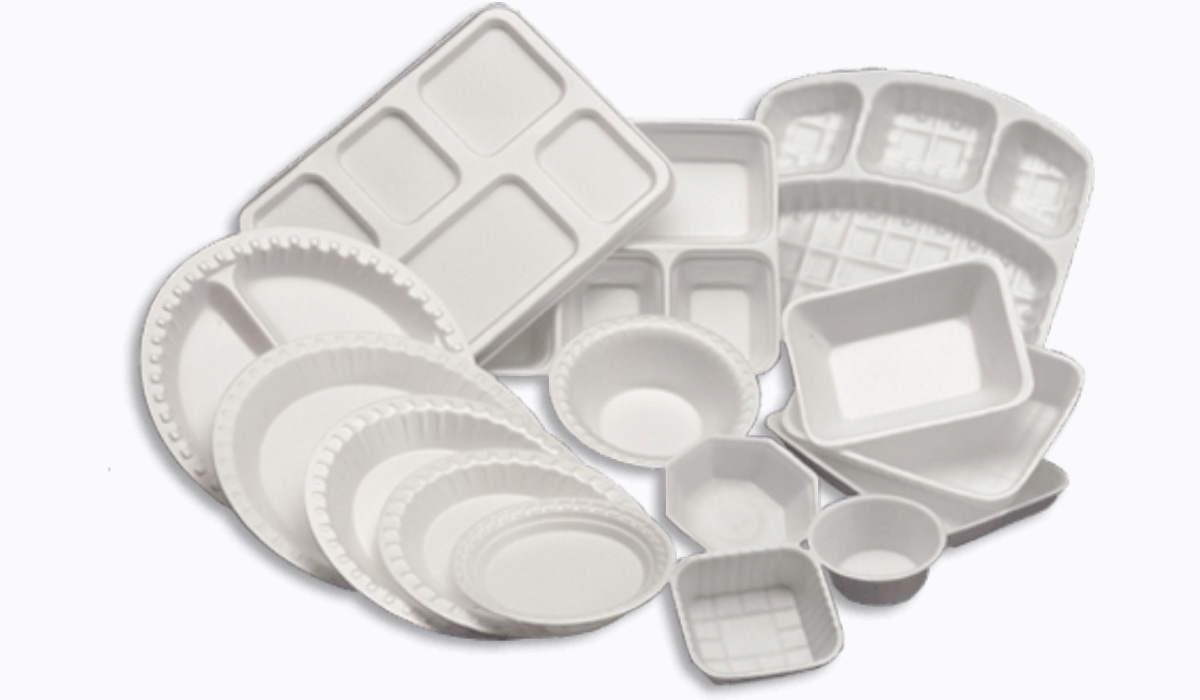
Thermoforming
- 🟢Disposable cups, trays for food.
- 🟢Product blister packs.
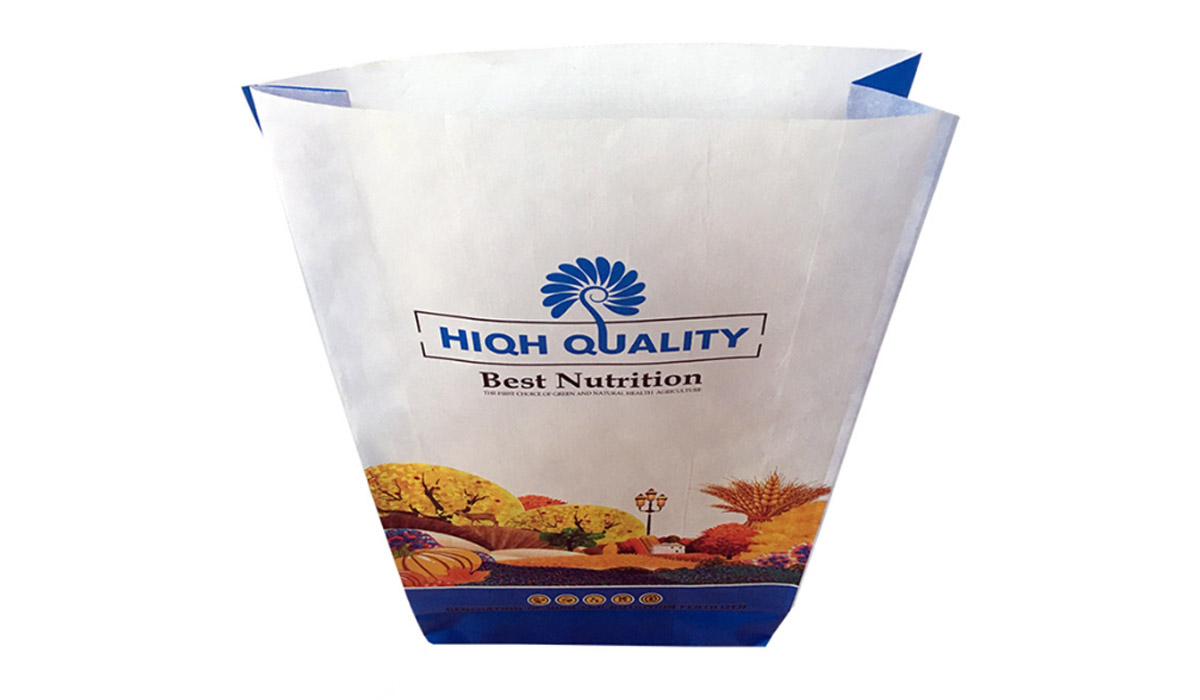
Lamination
- 🟢Used in the production of composite packaging.
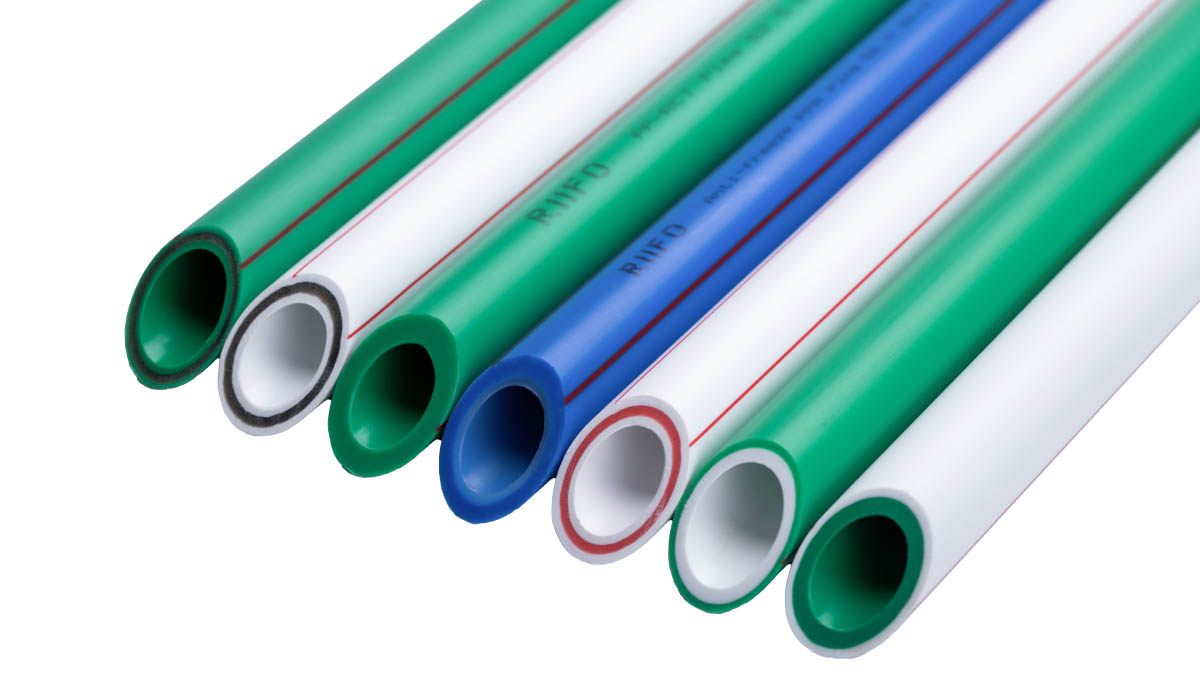
PPR Pipe
- 🟢PPR pipes for hot and cold water supply.
- 🟢PP sheets for partitions, file covers.
Your opinion matters to us. Share your thoughts, feedback, or inquiries by clicking the button below. Let’s start a meaningful conversation
Why Choose Mega Plast's CaCO3 Filler Masterbatch?
Megaplast stands out in the industry by owning both a limestone powder manufacturing plant and CaCO3 filler masterbatch production facility. This unique combination grants Megaplast a substantial competitive edge in the market. By controlling the entire production chain from raw limestone extraction to the final filler masterbatch product, Megaplast ensures unmatched quality control and product consistency. This vertical integration allows for a seamless adjustment of the CaCO3 powder’s properties to meet the specific requirements of filler masterbatch production, resulting in a superior product tailored to customer needs.
Furthermore, Megaplast’s direct access to raw materials significantly reduces production costs, enabling the company to offer highly competitive pricing without compromising quality. The close proximity of the limestone powder manufacturing plant to the filler masterbatch production facility minimizes logistics costs and environmental impact, contributing to more sustainable production practices.
Megaplast’s capability to rapidly respond to market demands and custom requirements is another advantage stemming from its integrated operations. The company can swiftly adapt its production processes to create custom formulations that meet specific customer needs, offering flexibility and innovation that are hard to match.
Overall, Megaplast’s dual operation of both a limestone powder manufacturing plant and a filler masterbatch production facility positions it as a leader masterbatch manufacturer in the industry, capable of delivering high-quality, cost-effective, and environmentally friendly solutions to a global clientele.